Not known Factual Statements About Alcast Company
Not known Factual Statements About Alcast Company
Blog Article
The Facts About Alcast Company Revealed
Table of ContentsAll about Alcast CompanyAlcast Company Can Be Fun For EveryoneThe Of Alcast CompanyThe Best Strategy To Use For Alcast CompanyTop Guidelines Of Alcast CompanyHow Alcast Company can Save You Time, Stress, and Money.
The subtle difference exists in the chemical content. Chemical Comparison of Cast Light weight aluminum Alloys Silicon promotes castability by decreasing the alloy's melting temperature level and improving fluidness throughout spreading. It plays an important function in permitting intricate molds to be loaded accurately. Additionally, silicon adds to the alloy's strength and use resistance, making it valuable in applications where toughness is crucial, such as vehicle parts and engine components.It also boosts the machinability of the alloy, making it much easier to refine into completed items. In this way, iron contributes to the general workability of aluminum alloys.
Manganese adds to the toughness of light weight aluminum alloys and boosts workability (aluminum metal casting). It is commonly made use of in functioned aluminum products like sheets, extrusions, and profiles. The presence of manganese help in the alloy's formability and resistance to splitting throughout fabrication processes. Magnesium is a light-weight element that provides stamina and effect resistance to aluminum alloys.
Unknown Facts About Alcast Company
Zinc boosts the castability of light weight aluminum alloys and helps manage the solidification procedure throughout casting. It improves the alloy's strength and solidity.
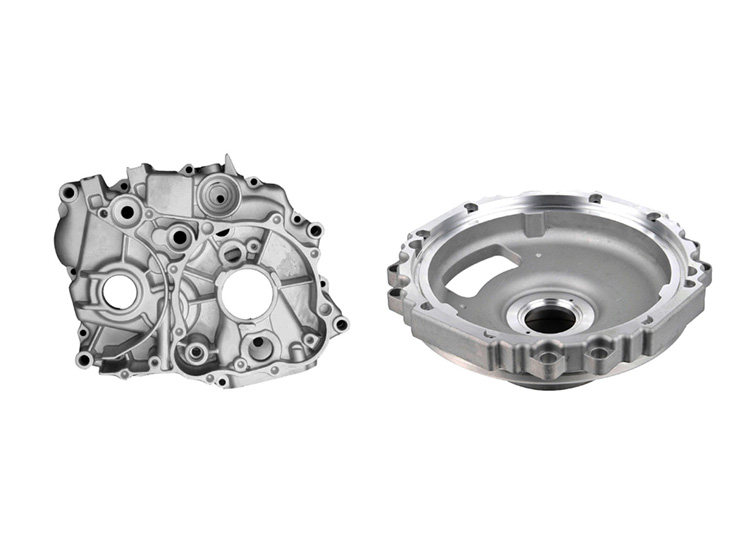
The main thermal conductivity, tensile strength, return toughness, and prolongation vary. Select suitable basic materials according to the performance of the target item created. Among the above alloys, A356 has the highest possible thermal conductivity, and A380 and ADC12 have the cheapest. The tensile restriction is the opposite. A360 has the best return strength and the highest possible prolongation price.
Getting The Alcast Company To Work
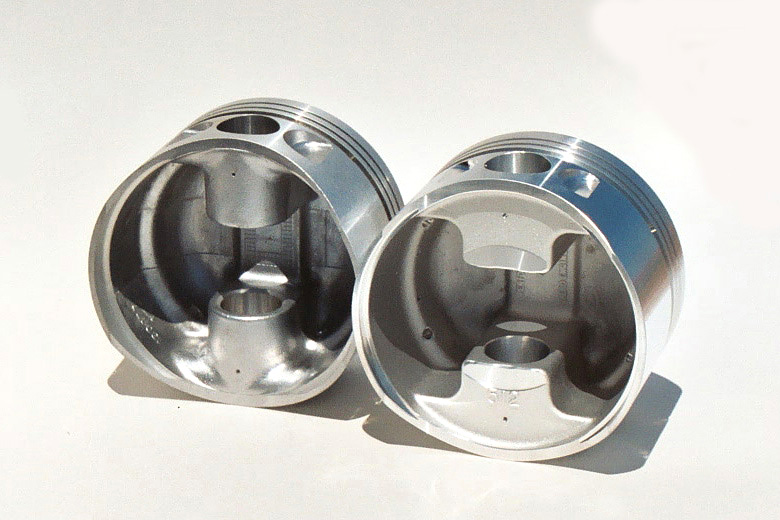
In precision casting, 6063 is appropriate for applications where detailed geometries and high-grade surface area coatings are critical. Instances include telecommunication enclosures, where the alloy's premium formability allows for smooth and visually pleasing designs have a peek at these guys while maintaining structural stability. In the Illumination Solutions market, precision-cast 6063 parts develop classy and efficient lighting fixtures that need intricate shapes and good thermal performance.
The A360 exhibits exceptional elongation, making it ideal for complex and thin-walled elements. In accuracy casting applications, A360 is appropriate for markets such as Consumer Electronic Devices, Telecommunication, and Power Devices.
9 Simple Techniques For Alcast Company
Its distinct residential or commercial properties make A360 a useful choice for accuracy casting in these sectors, enhancing product durability and high quality. Light weight aluminum alloy 380, or A380, is an extensively used casting alloy with numerous unique characteristics. It provides exceptional castability, making it an excellent option for accuracy spreading. A380 shows good fluidity when molten, making certain intricate and in-depth mold and mildews are properly reproduced.
In precision casting, aluminum 413 shines in the Consumer Electronics and Power Tools industries. It's typically used to craft complex elements like smartphone housings, electronic camera bodies, and power tool housings. Its precision is exceptional, with tight resistances as much as 0.01 mm, making sure perfect product assembly. This alloy's exceptional corrosion resistance makes it an outstanding choice for outside applications, ensuring durable, sturdy items in the stated markets.
Little Known Questions About Alcast Company.
The aluminum alloy you select will considerably affect both the spreading process and the residential properties of the last item. Because of this, you need to make your choice meticulously and take an enlightened approach.
Figuring out the most appropriate aluminum alloy for your application will imply weighing a large variety of characteristics. The initial category addresses alloy qualities that impact the manufacturing procedure.
An Unbiased View of Alcast Company
The alloy you choose for die casting directly impacts numerous facets of the spreading process, like how very easy the alloy is to deal with and if it is prone to casting flaws. Warm breaking, likewise known as solidification fracturing, is a typical die spreading problem for aluminum alloys that can result in internal or surface-level rips or cracks.
Particular aluminum alloys are more at risk to warm breaking than others, and your option ought to consider this. An additional usual issue discovered in the die spreading of aluminum is pass away soldering, which is when the actors stays with the die wall surfaces and makes ejection hard. It can harm both the actors and the die, so you need to seek alloys with high anti-soldering buildings.
Deterioration resistance, which is currently a noteworthy quality of light weight aluminum, can differ substantially from alloy to alloy and is a necessary particular to take into consideration relying on the environmental conditions your product will be subjected to (aluminum casting manufacturer). Put on resistance is an additional residential or commercial property frequently looked for in aluminum products and can distinguish some alloys
Report this page